Aluminium Coil Coating line, Galvanized Coil Coating line, CCL, Wall Clading Coil Coating line
This equipment is a machine that coats aluminum coil or galvanized coil. Production speed ranges from 30 m to 80 m per minute depending on the type of
Negotiable Min Order Quantity Unit
- Required Quantity
-
- Place of Origin
- South Korea
- Brand name
- Plama (I'm here for you)
- Payment Terms
- L/C
- Production method
- Available
- Shipping / Lead Time
- Negotiable / Negotiable
- Keyword
- color coating, coil coating line, galvanized line, ppgi line
- Category
- Other Paint & Coatings , Aluminum Composite Panels
PLAMA WORLDWIDE TECH CO., LTD
- Verified Certificate
-
16
Product name | Aluminium Coil Coating line, Galvanized Coil Coating line, CCL, Wall Clading Coil Coating line | Certification | - |
---|---|---|---|
Category |
Other Paint & Coatings
Aluminum Composite Panels |
Material | COIL COATING SECTION,COIL EXIT SECTION,Coil entry section,coil cleaning section |
Keyword | color coating , coil coating line , galvanized line , ppgi line | Unit Size | - |
Brand name | Plama (I'm here for you) | Unit Weigh | - |
origin | South Korea | Stock | 0 |
Supply type | Available | HS code | - |
Product Information
1. GENERAL DESCRIPTION
-THIS SPECIFICATION COVERS ONE COIL COLOR COATING LINE FOR PRODUCING VARIOUS COLOR COATED GIT (GAVANIZED IRON STEEL) COIL PRODUCTS. THESE LINES ARE CONSISTED OF ENTRY SECTION, DEGREASING SECTION, COATING SECTION INCLUDING OVEN AND COOLING DEVICES, EXIT SECTION, ELECTRICAL EQUIPMENT AND INSTRUMENTATION AS SHOWN ON DRAWING NO. PMOHCCL-09-000-00.
-WE HAVE PLENTIFUL TECHNICAL KNOWLEDGE AND EXPERIENCE REGARDING THE DESIGN, MANUFACTURE AND SUPERVISION OF INSTALLATION, COMMISSIONING, TEST RUNNING AND TRANING FOR COIL COLOR COATING LINE. WE ARE CONFIDENT OF SUPPLYING TO CUSTOMERS A COIL COLOR COATING LINE WHICH IS CAPABLE OF PRODUCING HIGH QUALITY PRODUCTS.
-BASICALLY, THE LINE WILL BE PLANNED TO OPERATE BY SEMI-AUTOMATIC METHODS.
2. MATERIAL CONDITION
1-1) RAW MATERIAL & LINE SPECIFICATION.
1) KINDS; HOT DIP GALVANIZED STEEL COIL(GIT)
MATERIAL |
ALUMINIUM COIL |
GI//GL/CR/EGI/GF COIL |
REMARK |
|
STRIP |
THICKNESS |
0.3-1.0mm |
0.15-1.2mm |
|
WIDTH |
700-1280mm |
600-1500mm |
|
|
LINE SPEED |
ENTRY |
0-85m/minute (12.5 sec) |
0-100m/minute |
STRIP (0.5 * 1250mm) |
PROCESS |
0-70m/min (12 sec) |
0-80m/min |
STRIP (0.5 * 1250mm) |
|
EXIT |
0-85/min |
0-100m/min |
STRIP (0.5 * 1250mm) |
MATERIAL |
ALUMINUM COIL |
GIT/EG/CR COIL |
REMARK |
|
ENTRY COIL |
INNER DIAMETER |
508mm |
508/600mm |
|
OUTER DIAMETER |
MAX. 1500mm |
MAX.1600mm |
|
|
COIL WEIGHT |
MAX. 8 ton |
MAX. 22 ton |
|
|
EXIT COIL |
INNER DIAMETER |
508mm |
508mm |
|
OUTER DIAMETER |
MAX.1500mm |
1600mm |
|
|
COIL WEIGHT |
MAX. 8 ton |
15 ton |
|
2) TENSILE STRENGTH. MAX. 50 kgs/mm2
MIN. 35 kgs/mm2
1-2) PRODUCTS.
1) KINDS.
-POLYESTER PRIMER COATING/EPOXY
-HIGH DURABLE POLYESTER, ACRYLIC COATING
-POLY VINYLIDENE FLUORIDE (PVdF) COATING
2) COIL WEIGHT. MAX. 15(GI) TON
3) COIL INSIDE DIAMETER. ∅508mm
4) COIL OUTSIDE DIAMETE. MAX. ∅1500mm
6) TENSILE STRENGTH. MAX. 50 kgs/mm2
MIN. 35 kgs/mm2
7) APPLICATION HOME APPLIANCE/CONSTRUCTION MATERIALS
1-3) REQUIREMENTS OF RAW MATERIAL SURFACE.
# ALUMINIUM ROLLED STRIPS AND COILS TO BE PROCESSED SHELL MEET THE FOLLOWING REQUIREMENTS.
(1) STRIPS SHALL HAVE THE SAME MACHANICAL PROPERTIES ALONG THE WHOLE LENGTH.
(2) STRIP SURFACE SHALL NOT HAVE(AVOID) ANY CRACK, DEEP SCRATCH AND DENT.
(3) QUANTITY OF ANTI-RUST OIL ON THE STRIPS SURFACE SHALL NOT BE MORE THAN 1,000mg/m2 BASED ON SIDE.
(4) WAVING OF STRIPS SHALL BE MAX. 0.5% AND HEIGHT IS LESS THAN 3mm POINT.
(5) ADMISSIBLE TRANSVERSE CURVE (CAMBER) SHALL BE LESS THAN 3 mm PER EACH 10m OF STRIP LENGTH.
(6) COILS SHALL BE BANDED IN ORDER TO PREVENT COIL’S PEELING WHILE TRANSPORTING.
(7) LENGTH TO BE SCRAPED SHALL BE MAX. 1 m AT THE TOP AND TAIL END EACH.
1-4) PRODUCT MIX TABLE (SIZE MIX) (UNIT; TON)
WIDTH THICK |
0.3 * T<0.4 |
0.4 * T<0.7 |
0.8 * T<1.0 |
SUM |
% |
800 * W<1000 |
200 |
400 |
400 |
1000 |
2.0 |
1000 * W<1100 |
2000 |
2500 |
4500 |
9000 |
20 |
1100 * W<1250 |
4000 |
6000 |
5000 |
15000 |
33 |
1250 * W<1600 |
6000 |
8000 |
6000 |
20000 |
45 |
TOTAL |
4700 |
8400 |
6900 |
45000 |
100 |
1-5) PRODUCTION SPEED
-ENTRY /EXIT. MAX. 100 m/min
-PROCESS MAX. 80 m/min (REAL PRODUCTION SPEED)
-THREADING SECTION MAX. 100m/min
1-6) BASIC SPECIFICATION
1) TYPE. COIL COLOR COATING LINE( 2 COATERS/ 2 BAKES)
2) PRODUCTION CAPACITY. MAX. 17.7 TON/HR FOR POLYESTER COATING WITH
0.37mmt ☓ 1,250mmw ☓ 80mpm ☓ 85%
2)PRODUCTION PLAN.
1) PRODUCTION PLAN.
-LINE SPEED 80 m/min
-CAPACITY CALCULATION OF CAPACITY BASED ON RAW MATERIAL.
# WORKING TIME (24 HRS); REFER TO 2-(2) OPERATION AND MAINTENANCE PLAN
-24HRS/DAY Ⅹ 365 DAYS =8,760 HRS/YEAR(AVERAGE RUNNING; 75%)
-1.25meterⅩ80m / minite Ⅹ 60 minute Ⅹ 6,570 hrs=39,420,000m2
1-7) BASIC DESIGN CONDITION
1) COATER UNIT
NOTE; THICKNESS ON ABOVE WILL BE DRY THICKNESS.
DESCRIPTION |
COATING THICKNESS(MICRON) |
SOLID VOLUME(%) |
|
PRIMER COATER |
TOP SURFACE |
MAX. 10 μ |
40 μ |
BOTTOM “ |
MAX. 5 μ |
40 μ |
|
FINISH COATER (PVdF WITH PAINT) |
TOP SURFACE |
MAX. 25 μ |
50 μ |
BOTTOM “ |
MAX. 5 μ |
40 μ |
(THS SOLID VOLUME WILL BE BEFORE THINNER MIX.)
2) CHEMICAL COATER UNIT
DESCRITPION |
COATING THICKNESS(WET) |
SOLID |
TOP |
3 g/m2 |
WATER BASE |
BOTTOM |
3 g/m2 |
WATER BASE |
## INCLUDED AUTOMATIC ROLL GAP CONTROLLER/NIP PRESSURE CONTROLLER.
##DUAL HEAD ROLLER COATER FOR QUICK PAINT CHANING.
3) OVEN UNIT
(1) DESIGN STANDARD (MAX. CAPACITY). 1.0mmt ☓ 1,500mmw ☓ 80m/minute(PVDF)
(2) PEAK METAL TEMPERATURE. OVEN 20℃ → 270℃
(3) OVEN LENGTH & ZONE & TEMP. NO. 2 FINISH OVEN; 20 m (3 ZONES)/20-270℃
-1 ZONE. 280℃ --PEAK METAL TEMPERATURE ; 120℃
-2 ZONE. 380℃--PEAK METAL TEMPERATURE; 200℃
-3 ZONE. 400℃--PEAK METAL TEMPERATURE; 270℃
(4) BAKING TIME(POLYESTER). PRIME OVEN 20 SECOND---AT 70 m/minute
FINISH OVEN 30 SECOND---AT 70 m/minute
(5) HOT AIR TEMPERATURE. MAX. 450℃
4) MIST & COOLER UNIT.
(1) DESIGN STANDARD. 1.0mmt ☓ 1,500 mmw ☓ 80m/minute
(2) METAL TEMPERATURE. NO.1 ;210℃ → 50 ℃ UNDER/ NO.2 ;250℃ → 50℃ UNDER
5) FUME INCINERATER (SPECIAL PARTS)
(1) TOTAL EXHAUST GAS FLOW RATE. MAX. 350 Nm3/minute
(2) SOLVENT LOAD. MAX. 110 kg / hr
(3) SOLVENT CALORIC VALUE. 9,000 kcal/ hr
(4) SOLVENT ENERGY. 1,350,000 kcal/ hr
(5) OPERATION TEMPERATURE. 750℃
(6) HEAT RECOVERY (HEAT EXCHANGER). 60% (810,000 kcal/ hr)
(DETAIL DATAS SHOULD BE PROVIDING FOR MORE EXACT CALCULATING FROM THE BUYER OWING TO THE COUNTRY STANDARD. IN THIS CANSE, INCINERATOR PRICE MAY INCREASE A LITTLE BITS.)
1-8) OPERATION CONDITION
(1) OPERATION MODE
OPERATION WILL BE CARRIED CONTINUOUSLY IN A SHIFT BY 3 GROUPS FOR 24 HOURS PER DAY.
(2) OPERATION AND MAINTENANCE PLAN MAY CHANGE OWING TO COUNTRY SITUATION.
DESCRIPTION |
COLOR & COATING LINE |
CALENDER HOURS |
24 hr ☓ 365 days= 8,760 hrs |
NON-OPERATION HOURS |
1,032 hrs |
MAINTENANCE |
840 hrs |
-ANNUAL REPAIR |
240 hrs (10 days ☓24 hrs) |
-PERIODICAL REPAIR |
1) 600 hrs (355/14 days/ TIME(25 days ☓24 hrs / TIME) 2) 192 hrs (8 days).----------------24 hr WORKING -NEW YEAR'S DAY; 3 DAY -LUNAR NEW YEAR; 2 DAYS -MAY DAY; 1 DAY -NATIONAL HOLIDAY THANKSGIVING DAY) ; 2 DAYS |
HOURS TO BE OPERATED |
7,668 hours |
OPERATION RATE |
75% |
NET OPERATION HOURS |
5,750 hrs |
|
|
◈ GENERAL DATA FOR CCL LINE
* CHAPTER 1. MAIN SPECIFICATION
-SECTION 1. GENERAL DESCRIPTION
-SECTION 2. MATERIAL & PRODUCT CONDITION
-SECTION 3. PRODUCTION PLAN
-SECTION 4. MAIN SPECIFICATION
-SECTION 5. FLOW CHART OF CCCL
-SECTION 6. WARRANTY FIGURE
* CHAPTER 2. SCOPE OF SUPPLY
-SECTION 1. GENERAL
-SECTION 2. OUT OF SCOPE
-SECTION 3. DIVISION OF SCOPE OF SUPPLY BETWEEN THE SELLER AND THE BUYER
-SECTION 4. CODES OF STANDARD
* CHAPTER 3. SPECIFICATION OF MECHANICAL EQUIPMENT
-SECTION 1. DETAIL SPECIFICATION
-SECTION 2. SPARE PARTS LIST
* CHAPTER 4. SPECIFICATION OF ELECTRICAL EQUIPMENT
-SECTION 1. ELECTRICAL EQUIPMENTS
-SECTION 2. MOTOR LIST
-SECTION 3. PROCESS CONTROL SYSTEM
-SECTION 4. OPERATOR CONTROL EQUIPMENT
-SECTION 5. SPECIFICATION OF INSTRUMENTATION EQUIPMENT
* CHAPTER 5. INSTRUMENTATION WORK, COMMISSIONING & TRAINING PROGRAM
-SECTION 1. SUPERVISION SERVICE
-SECTION 2. TRAINING PROGRAMS
1. GIS COIL COLOR COATING LINE WITH 2 COATERS & 2 BAKES FOR PRODUCTION OF VARIOUS COLOR COATED PRODUCTS.
♣ COIL COATING LINE FOR GALVANIZED IRON STEEL STRIPS.
-GIS COIL THICKNESS 0.15mm~~1.2mm
-COIL WIDTH 600mm ~~1500mm
-LINE SPEED 80 mt/minute
-COATING TYPE 2 COATED 2 BAKES
-OVEN TYPE GAS OVEN
-COIL WEIGHT 15 tons
-COATING MATERIAL POLYESTER AND PVdf
-WARRANTY PERIOD OF MAJOR COMPONENT FOR THIS MACHINE IS 24 MONTHS.
01. GALVANIZED IRON STEEL COIL ENTRY SECTION
01-1. NO. 1 & NO. 2 ENTRY COIL SKID 2 SETS
01-2. NO. 1 & NO. 2 ENTRY COIL CAR 2 SETS
01-3. NO. 1 & NO. 2 PAY-OFF REEL WITH SNUBBER ROLLS 2 SETS
01-4. NO. 1 & NO. 2 PINCH ROLL WITH THREADING TABLE 2 SETS
01-5. CARRY OVER TABLE 1 SET
01-6. ENTRY SHEAR UNIT 1 SET
01-7. DEFLECTOR ROLL 1 SET
01-8. SEAM WELDER 1 SET
01-9. NO. 3 PINCH ROLL 1 SET
01-10. NO. 1 BRIDE ROLL 1 SET
01-11. ENTRY LOOPER(ACCUMULATOR) 1 SET
01-12. NO. 1 STEERING ROLL WITH CPC UNIT & DEFLECTOR ROLL< EACH SET>
01-13. NO. 2 BRDIE ROLL 1 SET
01-14. ENTRY HYDRAULIC UNIT AND ENTRY ROLL
02. GALVANIZED IRON STEEL COIL CLEANING SECTION
02-15. DEGREASING UNIT 1 SET
02-16. BRUSH SCRUBBER UNIT 1 SET
02-17. NO. 1 HOT WATER RINSE 1 SET
02-18. NO.2 HOT WATER RINSE & SQUEEZE ROLL 1 SET
02-19. FUME EXHAUST DUCT 1 SET
02-20. NO.1 HOT AIR DRYER 1 SET
02-21. CHEMICAL COATER
02-22. NO.2 HOT AIR DRYER
02-23. FUME EXHAUST DUCT & FUME SCRUBBER
02-24. NO.3 BRIDE ROLL & ENTRY ROLL 1 SET
02-25. NO. 2 STEERING ROLL WITH EPC.
03. GALVANIZED IRON STEEL COIL COATING SECTION
03-26. NO.1 PRIMER(POLYESTER) COATER 1 SET
03-27. NO. 1(PRIME) OVEN UNIT WITH GAS OVEN SYSTEM 1 SET
03-28. NO.1 MIST WATER COOLER (QUENCHING) UNIT 1 SET
03-29. NO. 4. BRIDLE ROLL 1 SET
03-30. NO.3 STEERING ROLL WITH CPC UNIT 1 SET
03-31. FINISHING COATER 1 SET
03-32. FINISHING OVEN WITH GAS OVEN SYSTEM 1 SET
03-33. MIST COOLER(QUENCHING) UNIT 1 SET
03-34. GUIDE ROLL UNIT 1 SET
04. GALVANIZED IRON STEEL COIL EXIT SECTION
04-35. NO. 5 BRIDLE ROLL 1 SET
04-36. EXIT LOOPER(ACCUMULATOR)
04-37. NO. 5 STEERING ROLL WITH CPC UNIT 1 SET
04-38. NO. 6 BRIDE ROLL 1 SET
04-39. EXIT SHEAR UNIT 1 SET
04-40. EPC AND EXIT DEFLECTOR ROLL WITH EPC UNIT 1 SET
04-41. TENSION REEL 1 SET
04-42. BELT WRAPPER 1 SET
04-43. EXIT COIL CAR 1 SET
04-44. EXIT COIL SKID 1 SET
04-45. HYDRAULIC UNIT FOR EXIT COIL SKID
04-46. FUME INCINERATOR (OPTIONAL PARTS)
04-47. JOINT AND TENSION DETECTOR UNIT.
05. ELECTRICAL EQUIPMENT
-MACHINE MAIN CONTROL PANEL. 7 SETS.
-OPERATION PANEL. 5 SETS.
-OTHER CONTROL PANEL WITH IN-LINE. 10 SETS.
- Product Info Attached File
B2B Trade
Price (FOB) | Negotiable | transportation | Ocean Shipping |
---|---|---|---|
MOQ | Negotiable | Leadtime | Negotiable |
Payment Options | L/C | Shipping time | Negotiable |
PLAMA WORLDWIDE TECH CO., LTD
-
16
- President
- David-h RHYU
- Address
- (room 1224, Seogwipo-si, Jeju-do, Korea
- Product Category
- Other Construction Material Making Machinery,Other Packaging
- Year Established
- 1998
- No. of Total Employees
- 1-50
- Company introduction
-
Plama Worldwidetech Co., Ltd was established in 1998. In the early days of the business, wemanufactured and exported specially designed extruders, blow molding machines,and CCL (coil color coating) machines, and gained the respect and trust of manyoverseas customers. In addition, our company manufactures and exports speciallydesigned dipping machines to Southeast Asia, Central and South America, andAfrica. The demand for specially coated gloves is expanding as they arerequired in all industrial and construction sites and in the assembly processof precision machinery, including automobiles. The horizontal running type dipping machine is optimized for theproduction of PU, Nitrile (Glossy/Foam/Water Spray) coating gloves. TheVertical running dipping machine is optimized for the production of NitrileSandy fishing and Crinkle gloves. The countries we manufacture and supply toour customers abroad are Vietnam, Spain, Turkey, Chile, Uzbekistan, Ukraine,India, Russia, Iran, Argentina, Bangladesh, Sri Lanka.
Our goal is tobe a family for life, providing our customers not only with the best qualitymachines, but also with trust, faith, and credit. Our R&D center is stillworking today to develop new quality machines and equipment until all customersare satisfied. And the supply of all kinds of machines is accompanied byprofessional consulting service, including feasibility, engineering, totaldesign, training, and technical assistance.
- Main Markets
-
India
Indonesia
Kazakhstan
Russia
Turkey
- Main Product
- Attached File
Related Products
Air blast equipment
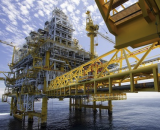
VCI Powder GVP100-B
__2.jpg)
119 PRODUCTS SERIES (Automatic fire suppression products)
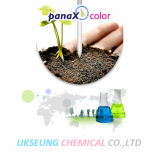
Panax Eco-Friendly Pigment
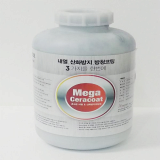
Cera Coat, Anti-corrosion coating, Liquid