ACID Regeneration Plant (SPR)
Negotiable Min Order Quantity Unit
- Required Quantity
-
- Place of Origin
- Payment Terms
- Negotiable
- Production method
- Negotiable
- Shipping / Lead Time
- Negotiable / Negotiable
- Keyword
- acid regeneration, hcl regeneration, spray roaster
- Category
- Other Machinery & Industry Equipment
ACREG GmbH
- Country / Year Established
-
Austria /
- Business type
- Others
- Verified Certificate
-
14
Product name | ACID Regeneration Plant (SPR) | Certification | - |
---|---|---|---|
Category | Other Machinery & Industry Equipment | Ingredients | - |
Keyword | acid regeneration , hcl regeneration , spray roaster | Unit Size | - |
Brand name | - | Unit Weigh | - |
origin | Stock | - | |
Supply type | - | HS code | - |
Product Information
The spent acid is concentrated in the gas separator using the hot gases of the reactor. The integrated venturi allows the elimination of iron oxide particles which escaped the cyclone because of their small grain size.
Finally, the concentrated solution of HCl and FeCl2 is injected into the reactor through spray nozzles at a pressure of 3 – 5 bar. The combustion inside the reactor usually happens at a surplus of air (λ>1).
Nearly all of the oxide produced (75-80%) drops down to the bottom of the reactor and is transported by a conveying system to the oxide storage bin. The residual part of the oxide fines are collected by a cyclone and returned to the reactor. The off gases of the spray roast process have a temperature of about 400°C. After leaving the cyclone these gases are cooled down by the venturi and the energy is used to preconcentrate the incoming pickling solution.
The process gases (now cooled down to around 100°C) pass through an adiabatic column to react with incoming water to 18% HCl. The incoming water gets added volumes of rinse waters from the pickling plant.
Additionally to this absorption system a chlorine scrubber can be applied, which acts as an effective means to extract minimum contents of chlorine gas created during the process. The combustion gases are further treated in a last scrubber column to eliminate residual HCl contents and oxide fines.
All process parameters are controlled automatically in order to maintain constant process conditions and thus constant acid and oxide quality. Oxide obtained from spray roasting technology is an essential and valuable resource for hard ferrite and pigment industry and can be obtained at low energy costs.
The advantages of the spray roast process are given in the lower energy costs compared with the fluidised bed process and the marketable red iron oxide (haematite).
B2B Trade
Price (FOB) | Negotiable | transportation | - |
---|---|---|---|
MOQ | Negotiable | Leadtime | Negotiable |
Payment Options | Negotiable | Shipping time | Negotiable |
- President
- Markus Österreicher
- Address
- Siebensterngasse 31/14, 1070 Vienna, Austria
- Product Category
- Other Machinery & Industry Equipment
- Main Product
Related Products
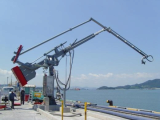
Marine Loading Arm
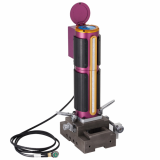
AIS3000 HD
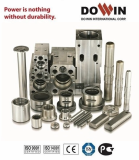
Spare Parts for Hydraulic Breaker
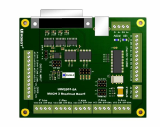
UIM2901-5A MACH3 break out board for CNC
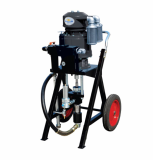
AIRLESS PUMP- YL 731